Implementation of a New Dosing Installation at a Confectionery Manufacturer
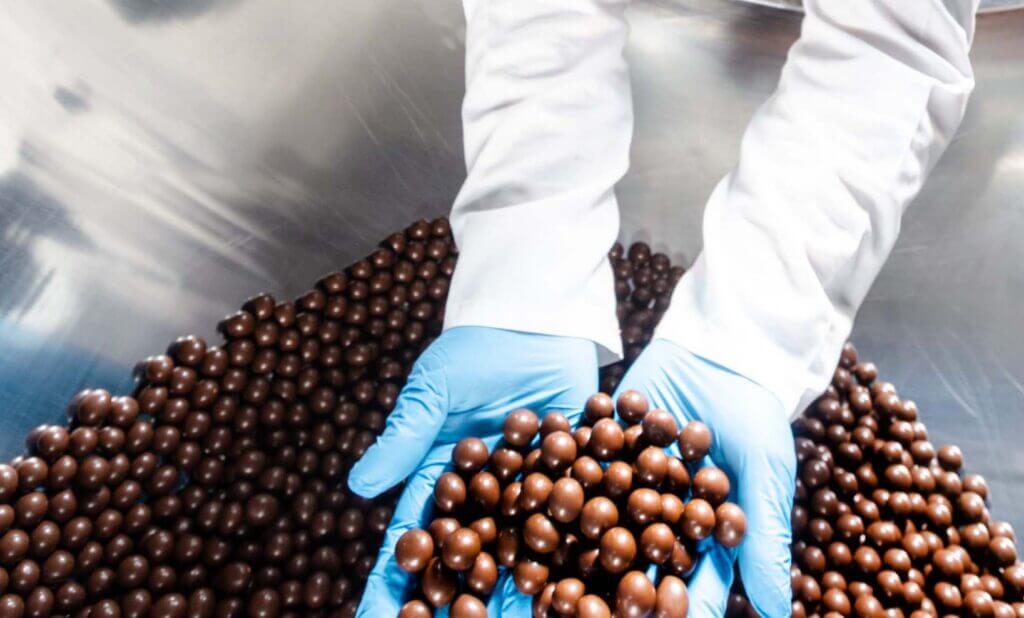
Protechnicon has successfully provided the detailed engineering for the implementation of a new dosing installation at a major confectionery manufacturer. The project focused on adding an emulsifier to the existing recipe, which presented some unique technical challenges.
Challenges and solutions
- Low Dosing Capacities: The installation had to dose very precise amounts of emulsifier, which required accurate and reliable equipment.
- Solidification properties of the Product: The emulsifier is liquid at 90°C and starts to solidify at 80°C, which required special attention to temperature control.
Complete Design and Implementation:
- Melting grid and temperature control: A new melting grid was installed for melting the product. The entire system is kept warm with tracing water at 90°C to prevent clotting.
- Process and Utility Systems: Protechnicon provided the complete engineering for both the process and utility systems, including all necessary calculations and component selection.
- Advanced 3D Scanning: We used advanced 3D scanning technology when creating the 3D drawings. This allowed the piping to be delivered completely prefabricated, resulting in minimal downtime during installation.
Collaboration and Multidisciplinary Teamwork:
We worked closely together within a multidisciplinary project team, where our expertise in both process technology and utilities was crucial to the success of the project.
Project duration
The entire process, from the initial design phase to the final implementation, was carried out within a tight timeline, ensuring the continuity of our customer’s production.
With this project, Protechnicon has shown that we can tackle and solve complex technical challenges within the confectionery sector. Our innovative approach and thorough engineering have led to a successful implementation of the dosing installation, resulting in an improved production process and increased efficiency for our customer.